Description
Early Equipment Management (EEM)
Continuous Improvement for Projects
Author: McCarthy Dennis
Language: Chinese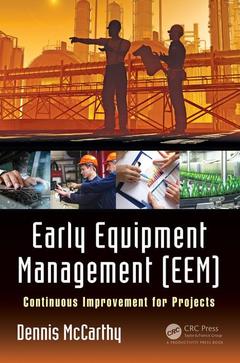
Subjects for Early Equipment Management (EEM):
Keywords
Glide Path; Total productive maintenance; Improve Supply Chain Responsiveness; capital projects; Design Module Structure; customer value; Flawless Operation; life-cycle cost; Expensive Computer Simulation Models; Operational Review; EEM; Stage Gate Review; LCC Management; RACI Chart; Fire Exits; LCC Model; Module Review Processes; Vice Versa; Stage Gate; NPD Project; Systematic Design Development; Organization’s Strategic Capability; Work Packet; Module Review; Criticality Assessment; Project Governance; Checklist Points; Improving Product Development Processes
· 15.6x23.4 cm · Hardback
Description
/li>Contents
/li>Readership
/li>Biography
/li>
When capital projects fail to deliver, it is usually not due to technical reasons but a combination of behavioral pitfalls, unclear accountabilities and gaps in design, specification, and/or project-management processes.
Early Equipment Management (EEM): Continuous Improvement for Projects explains how well known and award winning organizations avoid these weaknesses by using:
- Project road maps setting out clear accountabilities for each step of the concept-to-project-delivery process;
- Progressive design goals for each step to assure the delivery of low life-cycle costs;
- Processes to codify tacit knowledge, reveal latent design weaknesses, and build high performance cross-functional team collaboration;
- Project governance processes that systematically raise their organizations ability to reduce time to market for new assets, products and services with higher added value and fewer resources. Hence the books title of continuous improvement for projects.
The word Early in EEM refers to the principle of trapping problems as early as possible in the project process when they are cheapest to resolve. That makes EEM relevant to all projects even those that have past the design stages. To support the use of EEM at any project step, the author has designed each chapter as a standalone topic with cross references to other chapters where relevant. This book:-
- Explains
- The six EEM project delivery steps setting out the tasks and accountabilities for project teams, project managers and steering committees at each step;
- How to organize projects to increase project added value through the collaboration of commercial, operational and technology stakeholders
- The wiring up behind behaviors that contribute to the failure of traditional project management approaches and how to avoid those pitfalls;
- The use of projects as a vehicle for the development of internal talent and increase capital project added value
- The systematic development of internal capabilities to deliver flawless operation from day one in less time with less resources
- How raising project governance capability directly impacts on company wide management competence
- Uses case studies to explain how to implement the EEM methodology and
- Describes how EEM principles and techniques applied to product and service development (Early Product Management) multiplies the gains from EEM.
This book shows readers how and why EEM works so that they can design their own EEM road map and continuous improvement process for projects.
Contents
Preface
Chapter 1: Early Equipment Management
Delivering Capital Projects Faster, Cheaper, Better
1.1 What goes wrong?
Steps 1 and 2: Before EEM
Change curve
Cost curve
Steps 3 and 4 Before EEM
Change curve
Cost curve
Steps 5 and 6 Before EEM
Change curve
Cost curve
What is really happening
The Voyage of Discovery
1.2 EEM in action
Steps 1 and 2 With EEM
Change curve
Cost Curve
Steps 3 and 5 With EEM
Change curve
Cost Curve
Steps 5 and 6 With EEM
Change curve
Cost Curve
The gains
1.3 Why we need EEM
Understanding Project Delivery Weaknesses
D. Collaboration Weaknesses
This is a symptom of poor working relationships/collaboration. That can mean that weak ideas are untested until it is too late resulting in unforeseen (but predictable) Installation and commissioning problems.
Making Better Decision
Project Governance
Knowledge Management:
Delivering better management processes
1.4 The Book Structure
Overview
Chapter Summaries
Chapter 2: The EEM Road Map
2.1 EEM Road Map Overview
Define: Getting the Right Design
Design: Getting the design right
Refine: Getting the Design Gains
Improve
2.2 EEM Project Work Streams RACI
RACI: Responsible
2.3 RACI Accountable Column: Design Phase
Concept development: Aim, to develop a preferred concept
High Level Design: Aim, to approve funding and the basis for vendor selection
2.4 RACI Accountable Column: Design Phase
Detailed Design: Aim, to develop a detailed specification and project delivery programme.
Prefab Procurement
2.5 RACI Accountable: Refine Phase
Step 5: Installation: Aim, to install equipment in plant
Step 6 Commissioning: Aim, to deliver flawless operation on production day 1
2.6 RACI Accountable: Improve Phase
Step 7 Stabilise
Step 8 Optimise
2.7 Summary
Chapter 3: Design and Performance Management
3.1 In search of better design
Innovation
Systematic Design Development
3.2 In search of better performance
Criticality assessment
Hidden Loss Analysis/Trouble Map
Condition Appraisal
Day in the Life of (DILO)Review
Incorporating PP data in Design
3.3 Avoiding Design Pitfalls
Create Design Modules
Recognise Vendor Skill Sets
Understand Behavioural Bias
Apply the EEM Design Hierarchy
Design Goals
Design Guidelines
Technical Standards
Objective Testing
Integrating Stakeholder Workstreams
3.4 Systematic Design Development: Define Phase
3.5 Systematic Design Development: Design Phase
Vendor Induction
Detailed design workshops
Problem Prevention
Detailed activity planning
3.6 Systematic Design Development: Refine and Improve
3.7 Chapter Summary
Chapter 4: Specification and LCC Management
4.1 Having the Right Conversations
Keep the conversation flowing
Setting the Design Agenda
Checklist Management
4.2 Creating powerful specifications
Layouts
Module Review
Approach
Value Engineering Review
Preparation
Approach
Resource Management/Systems specification
Draft Specification
Systems High Level Design
Systems Detailed Design and Forward Program
User training, Systems Validation and Go live
Setting Design Targets
Process Milestones
Basic Life Cycle Cost Model Example
Estimating Costs
Operating Cost Estimates
Capital cost estimates.
ITT Design
Approach
Process Milestone
4.3 Detailed Design
Module Review Update
Dealing with Risk
Specify low risk solutions
Specify Problems to be prevented
Use Charts and Graphs to Raise Awareness
Specify Learning Plans that Reduce Error Risks
Detailed Activity Planning
Change Control
Witnessed inspection
4.4 Define
4.5 Design
4.6 Refine and Improve
Day One Production and Site Acceptance Testing
4.7 Summary
Chapter 5: Project and Risk Management
5.1 Developing the project plan
Milestone Planning
Understanding the critical path
Communicating Project Timelines
Work Scheduling
5.2 Managing people and teams
Creating the Collective Team Vision
Team induction
Team Dynamics
Collaborating with Vendors
Managing Communication Processes
Project Administration
Personal systems and procedures
5.3 Managing risk
The Purpose of Risk Management
Surfacing Hazards
Registering Risks
Highly Regulated Industries
Implementing Risk Mitigation
5.4 Define
Project Leader Role: Concept
Project Leader Role: High Level design
5.5 Design
Project Leader Tasks: Detailed Design
Project Leader Role: Pre Fab Procurement
5.6 Refine and Improve
Project Leader Role: Installation
Project Leader Role: Commissioning
Project Leader Role Stabilise
5.7 Chapter summary
Chapter 6: Project Governance
Impact of Internal Processes
6.1 Project Governance: Mind Set and Skill Set
Direction Setting
Capability Building
Performance Management
Vendor Performance
Results Delivery
6.2 Organisational Development, The Leadership Challenge
Setting EEM Policies
EEM Policy Example
Policy and Direction
Project Delivery
EEM Support
EEM Subject Matter Expert
Project Manager/Installation Manager
Best Practice Design book
6.3 Organisational Development: Measuring Progress
Setting targets
Beyond the Stage Gate Review
Stage Gate Team Coaching Role
Coaching parallel work streams
EEM Audit Process
Approach
Audit Roles
Audit Agenda
Task Milestones
6.4 Locking in the EEM Gains
The Origins of EEM
Best Practice Design Books
Compatibility of EEM with Other Design Tools
6.5 Define
Concept Stage Gate
High Level Design Stage Gate
6.6 Design
Detailed Design
Pre Fab Procurement
6.7 Refine and Improve
Installation
Commissioning
Post Day 1: Stabilise
6.8 Chapter summary
Chapter 7: Implementing EEM
7.1 Define
Planning and preparation
Management Awareness
Mobilisation
7.2 Design
Pilot
Policy Development
7.3 Refine
7.4 Improve
EEM Subject Matter Expert Learning Pathways
7.5 Speeding up time to market
Design and Performance Management Processes
Specification and LCC Management:
Project and Risk Management Processes
Project Governance
Best Practice Design Book Processes
7.6 Chapter Summary
Chapter 8: Early Product Management
Why do we need EPM?
What is EPM?
EPM Road Map
8.1 EPM Step 1: Shell
8.3 EPM Step 2: Shape
Design and Performance Management Issues
Specification and LCC Management Process
Project and Risk Management Process
8.4 EPM Step 3: Scope
Design and Performance Management
Specification and LCC Management
Project and Risk Management
8.4 Links with EEM
Project Governance
Design and Performance Management
Specification and LCC Management
Project and Risk Management
8.5 Implementing EPM
8.6 Chapter Summary
Dennis McCarthy began his career as an Industrial Engineer and led a number of major Logistics projects. He progressed to European Project Manager for a US Multinational managing pan European Manufacturing, Logistics and IT projects. As a consultant he as supported Manufacturing improvement programmes ranging in size from small single site applications to companywide multi-site transformation programmes in Europe, USA, India and China. This has included support for well-respected and award winning companies such as 3M, Ford, General Motors, Heineken, Pepsi, Rolls Royce and Ikea. He has co-authored 2 books published by Butterworth Heinemann. TPM a route to world class, Lean TPM a blueprint for change.