Description
Ceramics, 1999
Mechanical Properties, Failure Behaviour, Materials Selection
Coll. Springer Series in Materials Science, Vol. 36
Authors: Munz Dietrich, Fett Theo
Language: French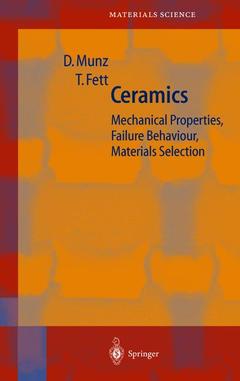
Subject for Ceramics:
Keywords
ceramics; deformation; fatigue; fracture; fracture mechanics; mechanics; plastic deformation; plasticity; stress
Ceramics, Mechanical Properties, Failure Behaviour, Materials Selection (POD)
Publication date: 10-2012
299 p. · 15.5x23.5 cm · Paperback
Publication date: 10-2012
299 p. · 15.5x23.5 cm · Paperback
Ceramics: mechanical properties, failure behaviour, materials selection (Springer series in materials science vol 36)
Publication date: 03-1999
299 p. · 15.5x23.5 cm · Hardback
Publication date: 03-1999
299 p. · 15.5x23.5 cm · Hardback
Description
/li>Contents
/li>Comment
/li>
Ceramic materials are widely used as components in a great variety of applications. They are attractive due to their good high temperature strength, high wear resistance, good corrosion restistance and other special physical properties. Their major drawback is their brittleness and the large scatter of their mechanical properties. This book describes failure phenomena in ceramic materials under mechanical loading, methods for determining the material properties, and the principles that one should apply when selecting a material. The fracture-mechanical and statistical principles and their use in describing the scatter of strength and lifetime are also covered. Special chapters are devoted to creep behaviour, multiaxial failure criteria and thermal shock behaviour.
1 Overview and Basic Properties.- 1.1 General Behaviour.- 1.2 Overview of Ceramic Materials.- 1.3 Fields of Application.- 2 Physical Properties.- 2.1 Thermal Expansion Coefficient.- 2.2 Thermal Conductivity.- 2.3 Electrical Conductivity.- 2.4 Specific Heat.- 2.5 Density.- 2.6 Elastic Constants.- 3 Fracture Mechanics.- 3.1 Fundamentals.- 3.2 Experimental Methods for the Determination of the Mode-I Fracture Toughness KIc.- 3.3 Experimental Methods for the Determination of Mode-II and Mixed-Mode Fracture Toughness.- 3.4 Mixed-Mode Criteria and Experimental Results.- 4 R-Curve Behaviour.- 4.1 Experimental Observation.- 4.2 Determination of R-Curves.- 4.3 Reasons for R-Curve Behaviour.- 4.4 Influence of R-Curves on Strength.- 4.5 Computation of R-Curves.- 4.6 Determination of Bridging Stresses from Crack Profiles.- 5 Subcritical Crack Growth.- 5.1 Basic Relations.- 5.2 Computation of Lifetimes.- 5.3 Methods of Determining Subcritical Crack Growth.- 5.4 Influence of R-Curve Behaviour on Subcritical Crack Growth.- 5.5 Some Theoretical Considerations on Subcritical Crack Growth.- 6 Cyclic Fatigue.- 6.1 Representation of Cyclic Fatigue Results.- 6.2 Proof of a Cyclic Effect.- 6.3 Methods for the Determination of da/dN-?K Curves.- 6.4 Effect of R-Ratio.- 6.5 Theoretical Considerations.- 6.6 Differences Between Micro- and Macrocracks.- 7 Determination of Strength.- 7.1 Measurement of Tensile Strength.- 7.2 Measurement of Compressive Strength.- 8 Scatter of Mechanical Properties.- 8.1 Principal Behaviour.- 8.2 Determination of Weibull Parameters.- 8.3 The Size Effect.- 8.4 Scatter of Lifetimes.- 8.5 Some Specific Problems.- 9 Proof Test Procedure.- 9.1 Proof Test Without Subcritical Crack Growth.- 9.2 Proof Test Including Subcritical Crack Growth.- 9.3 Problems in Proof Tests.- 10Multiaxial Failure Criteria.- 10.1 Representation in Multiaxiality Diagrams.- 10.2 Global Multiaxiality Criteria.- 10.3 Defect Models.- 10.4 Experimental Methods.- 10.5 Experimental Results.- 11 Thermal Shock Behaviour.- 11.1 Thermal Stresses.- 11.2 Measurement of Thermal Shock Sensitivity.- 11.3 Fracture Mechanical Treatment of Thermal Shock.- 11.4 Thermal Shock Parameters.- 11.5 Size Effect in Thermal Shock.- 11.6 Thermal Fatigue.- 12 High-Temperature Behaviour.- 12.1 Creep Deformation.- 12.2 Failure in the Creep Range.- 12.3 Creep Crack Growth.- 13 Plasticity.- 13.1 Plasticity During Contact Loading.- 13.2 Plasticity During Surface Grinding.- 13.3 Plasticity by Phase Transformation in Zirconia.- 13.4 Plasticity by Domain Switching in Piezoelectric Ceramics.- 13.5 Measurement of Plastic Deformations in Bending Tests.- 13.6 Time-Dependent Plasticity Effects.- A.1 Rectangular Bar.- A.2 Comact-Tension (CT) Specimen.- A.3 Round Compact Tension (RCT) Specimen.- A.4 Double-Cantilever-Beam Specimen (DCB).- A.5 Weight Function for Chevron-Notched Bending Bars.- A.6 Specimens for Mixed-Mode Tests.
The special methods of component design with ceramic materials are presented Applying these methods the engineer is enabled to design ceramic components in a reliable way Includes supplementary material: sn.pub/extras
© 2024 LAVOISIER S.A.S.