Description
Fatigue of Textile and Short Fiber Reinforced Composites
Authors: Carvelli Valter, Jain Atul, Lomov Stepan
Language: English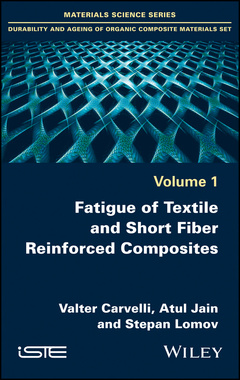
Subject for Fatigue of Textile and Short Fiber Reinforced Composites:
Keywords
contents; composites; fatigue; behavior; evolution; experimental; composite; eglass; plain; epoxy; textilereinforced; observation; quasistatic tensile; properties
171.59 €
In Print (Delivery period: 14 days).
Add to cart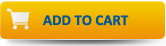
224 p. · 15.8x23.4 cm · Hardback
Description
/li>Contents
/li>Biography
/li>
The second part is devoted to the fatigue behavior of injection molded short fiber reinforced composites. Experimental evidence highlights the dependence of their fatigue response on various factors: fiber and matrix materials, fiber distribution, environmental and loading conditions are described. A hybrid (experimental/simulations) multi-scale method is presented, which drastically reduces the amount of experimental data necessary for reliable fatigue life predictions.
Preface ix
Part 1 Fatigue of Textile Composites 1
Chapter 1 Fatigue Behavior and Damage Evolution of 2D and 3D Textile-Reinforced Composites 3
1.1 Introduction 3
1.2 Experimental methodologies 5
1.3. Fatigue behavior and damage evolution in 2D E-glass plain weave textile-reinforced epoxy composite 9
1.3.1 Quasi-static tensile behavior and damage observation 10
1.3.2 Fatigue life and damage metrics 15
1.3.3 Fatigue damage observation and evolution 18
1.3.4 Postfatigue mechanical properties and damage observation 21
1.4 Fatigue behavior and damage evolution in single-ply non-crimp 3D orthogonal weave E-glass reinforced epoxy composite 24
1.4.1 Quasi-static tensile behavior and damage observation 26
1.4.2 Fatigue life and damage metrics 34
1.4.3 Fatigue damage observation and evolution 40
1.4.4 Postfatigue mechanical properties and damage observation 44
1.5 Fatigue behavior and damage evolution in 3D rotary braided carbon reinforced epoxy composite 49
1.5.1 Quasi-static tensile behavior and damage observation 51
1.5.2 Fatigue life and damage metrics 55
1.5.3 Fatigue damage observation and evolution 58
1.5.4 Postfatigue mechanical properties 60
1.6 Fatigue behavior and damage evolution in non-crimp stitched and unstitched carbon reinforced epoxy composite 63
1.6.1 Quasi-static tensile behavior 64
1.6.2 Fatigue life and damage metrics 67
1.6.3 Fatigue damage observation and evolution 71
1.6.4 Postfatigue mechanical properties 73
1.7 Remarks and perspectives 78
1.8 Bibliography 80
Chapter 2 Fatigue Limit: A Link to Quasi-Static Damage? 87
2.1 Fatigue limit 87
2.2 Damage development stages and load thresholds for quasi-static tension 90
2.3 Damage development in quasi-static tension and in the progression of fatigue loading 93
2.4 Experimental data on the fatigue limit and the quasi-static damage thresholds for textile composites 96
2.4.1 Fatigue limit for glass fiber reinforced composites 98
2.4.2 Fatigue limit for carbon fiber reinforced composites 100
2.5 Summary and conclusion on the fatigue life limit 102
2.6 Bibliography 104
Part 2 Fatigue of Short Fiber Reinforced Composites 107
Chapter 3 Experimental Observations of Fatigue of Short Fiber Reinforced Composites 109
3.1 Injection molded SFRC 110
3.2 SN curve behavior of SFRC 113
3.2.1 Fiber-based parameters 115
3.2.2 Loading-based parameters 121
3.2.3 Environmental effects 123
3.2.4 Specimen configurations 125
3.3 Loss of stiffness 127
3.3.1 Collection of loss of stiffness data 131
3.3.2 Comparison of the loss of stiffness curves 133
3.4 Future outlook and modeling strategy 136
3.5 Bibliography 137
Chapter 4 Fatigue Modeling of SFRC: A Master SN Curve Approach 145
4.1 Overall framework and modeling strategy 145
4.2 Choice of a mean field homogenization method 151
4.2.1 Benchmarking of schemes with full FE solution 153
4.3 Damage modeling 157
4.3.1 Fiber–matrix debonding: equivalent bonded inclusion approach 159
4.3.2 Matrix damage 163
4.3.3 Validation 163
4.4 MSNC approach 165
4.4.1 Scaling of SN curves using the endurance limit 166
4.4.2 MSNC approach 168
4.4.3 Validation 173
4.4.4 Comparison of the MSNC scheme with other schemes 177
4.5 Component-level simulations 181
4.6 Conclusions and future outlook 184
4.7 Bibliography 185
Index 195
Atul Jain, Institute of Technology, India.
Stepan Lomov, University of Leuven (KU Leuven), Belgium.