Description
Machine Tool Practices (11th Ed.)
Authors: Kibbe Richard, Meyer Roland, Stenerson Jon, Curran Kelly
Language: English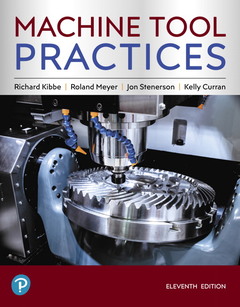
Subject for Machine Tool Practices:
221.11 €
In Print (Delivery period: 14 days).
Add to cart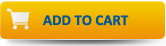
800 p. · 10x10 cm · Hardback
Description
/li>Contents
/li>Biography
/li>Comment
/li>
The all-in-one solution for teaching machining, BPR, GD&T, and CNC courses
Machine Tool Practices provides clear, practical, and richly illustrated treatment of machine tool technology and prepares students for NIMS certification. Vast in breadth and depth, this is the definitive text for training computer numerical controllers, conventional machine operators, general machinists, and tool and tie makers. The 11th edition includes dramatically expanded content and supplements on blueprint reading, GD&T, and CNC, giving it the potential to be the sole source of material for courses on these topics, while saving students the expense of two extra texts.
SECTION A
1. Careers and the Machinist's Role in Process Plans
2. Manufacturing Competitiveness and Improvement
3. Shop Safety
4. Threads and Fasteners
5. Blueprint Reading Fundamentals
6. Views and Line Types
7. Dimensions, Tolerances, and Fits
8. Fundamentals of GD&T
9. Geometric Tolerancing
SECTION B: HAND TOOLS
1. Arbor and Shop Presses
2. Work-Holding and Hand Tools
3. Hacksaws
4. Files
5. Hand Reamers
6. Identification and Uses of Taps
7. Tapping Procedures
8. Thread-Cutting Dies and Their Uses
9. Off-Hand Grinding
SECTION C: DIMENSIONAL MEASUREMENT
1. Measurement and Common Measuring Tools
2. Systems of Measurement
3. Using Steel Rules
4. Using Vernier, Dial, and Digital Instruments for Direct Measurements
5. Using Micrometers
6. Using Comparison Measuring Instruments
7. Using Gage Blocks
8. Using Angular Measuring Instruments
9. Quality in Manufacturing
10. Statistics in Manufacturing
SECTION D: MATERIALS
1. Selection and Identification of Steels
2. Selection and Identification of Nonferrous Metals
3. Hardening, Case Hardening, and Tempering
4. Annealing, Normalizing, and Stress Relieving
5. Rockwell and Brinell Hardness Testers
SECTION E: LAYOUT
1. Layout Tools
2. Basic Semiprecision Layout Practice
3. Basic Precision Layout Practice
SECTION F: PREPARATION FOR MACHINING OPERATIONS
1. Machinability and Chip Formation
2. Speeds and Feeds for Machine Tools
3. Cutting Fluids
4. Carbide Tooling Specification and Selection
SECTION G: SAWING MACHINES
1. Types of Cutoff Machines and Safety
2. Using Horizontal Cutoff Saws
3. Preparing a Vertical Band Machine for Use
4. Using a Vertical Band Saw
SECTION H: DRILLING MACHINES
1. Drill Press Fundamentals
2. Drilling Tools
3. Hand Grinding of Drills on the Pedestal Grinder
4. Operating Drilling Machines
5. Countersinking and Counterboring
6. Reaming in the Drill Press
SECTION I: TURNING MACHINES
1. Engine Lathe Fundamentals
2. Toolholders and Toolholding
3. Cutting Tools for the Lathe
4. Lathe Spindle Tooling
5. Operating Lathe Controls
6. Facing and Center Drilling
7. Turning between Centers
8. Alignment of Lathe Centers
9. Other Lathe Operations
10. Sixty-Degree Thread Information and Calculations
11. Cutting Unified External Threads
12. Cutting Unified Internal Threads
13. Cutting Tapers
14. Using Steady and Follower Rests
15. Additional Thread Forms
16. Cutting Acme Threads on the Lathe
SECTION J: VERTICAL MILLING MACHINES
1. Vertical Milling Machines
2. Cutting Tools and Cutting Tool Holders for the Vertical Milling Machine
3. Setups on the Vertical Milling Machine
4. Vertical Milling Machine Operations
5. Using an Offset Boring Head
SECTION K: HORIZONTAL SPINDLE MILLING MACHINES
1. Horizontal Spindle Milling Machines
2. Types of Spindles, Arbors, and Adapters
3. Arbor-Driven Milling Cutters
4. Work-Holding Methods and Standard Setups
5. Machine Setup and Plain Milling
6. Using Side Milling Cutters
SECTION L: GRINDING AND ABRASIVE MACHINING PROCESSES
1. Types of Grinders
2. Selection and Use of Grinding Wheels
3. Setup of Surface Grinders
4. Using a Surface Grinder
5. Cylindrical Grinding
6. Using a Cylindrical Grinder
7. Universal Tool and Cutter Grinder
SECTION M: COMPUTER NUMERICAL CONTROL AND OTHER ADVANCED MACHINING PROCESSES
1. Fundamentals of Computer Numerical Control (CNC)
2. Fundamentals of Machining Centers
3. Fundamentals of Programming Machining Centers
4. Programming Examples
5. Programming Canned Cycles for Machining Centers
6. CNC Turning Machines
7. Programming CNC Turning Centers
8. Programming Canned Cycles for CNC Turning Centers
9. Advanced Machining Processes
About our authors
Jon Stenerson served an apprenticeship in toolmaking with Mercury Marine and was an instructor in the Machine Tool Program at Fox Valley Technical College (FVTC) in Appleton, WI. An industry consultant, Jon is the author of textbooks in the fields of machining, CNC programming and industrial automation. He has a BBA from the University of Wisconsin Oshkosh and a master's degree in vocational education from the University of Wisconsin-Stout.
Kelly S. Curran grew up in Michigan's Upper Peninsula, where he started working in machine shops at a young age. Mr. Curran has considerable machine shop experience as well as industrial teaching experience. He is the author and coauthor of several publications in the machine tool manufacturing field. Mr. Curran has spent many years developing a self-paced machine tool curriculum for the State of Wisconsin and Fox Valley Technical College. He holds a bachelor's degree in career, technical education and training from the University of Wisconsin-Stout, an associate of applied science degree with an emphasis in machine tool from Ferris State College, and an associate of applied science degree with an emphasis in business from Northern Michigan University.
Hallmark features of this title
Features and rich illustrations with tips and techniques
- Extensive use of hundreds of color photographs provides students with views of actual machining operations.
- Graphic explanations highlight important concepts, common errors and difficulties encountered by machinists.
Learning aids
- Shop Tip and Shop Tip Craftsmanship boxes offer tips and techniques to help students become intuitive machinists.
- End-of-unit self-tests gauge student mastery of the material.
These books may interest you
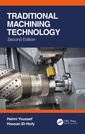
Traditional Machining Technology 208.65 €
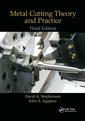
Metal Cutting Theory and Practice 111.58 €
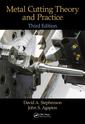
Metal Cutting Theory and Practice 281.07 €